What are the process details that must be mastered in offset printing production?
Time:2025-07-08
Views:411
The offset printing process involves both physical and chemical aspects, which require a high level of mastery of the process and technology. Often, due to issues with the process and technical level of management and operators, there are also many offset printing failures.
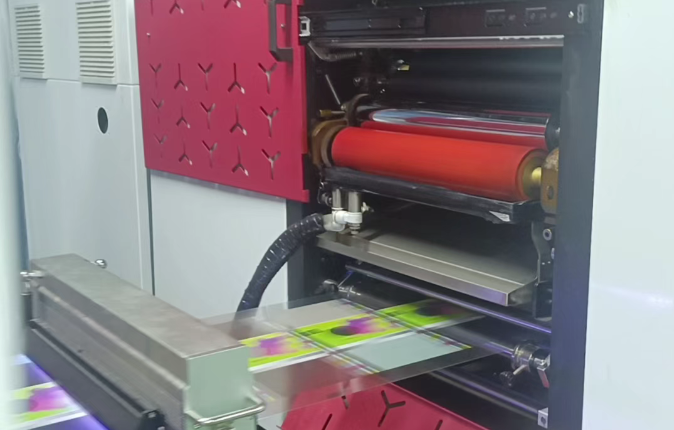
Offset printing characteristics
Offset printing uses the principle of oil and water repelling to print on the same printing plate. The graphic and textual parts are hydrophilic and hydrophobic, while the blank parts are hydrophilic and hydrophobic. This is the most obvious difference between offset printing and other printing methods, and it is also the key to offset printing technology.
In the presence of both ink and water on the printing plate, the ink roller that transports the ink comes into contact with water. Due to the high-speed rotation of the ink roller and the squeezing effect of mechanical force, water is mixed into the ink, causing ink emulsification. In normal printing, a reasonable emulsification value is achieved. Therefore, offset printing actually utilizes both the principle of oil and water repulsion and the characteristic of oil and water solubility emulsification.
According to foreign experimental data, when offset printing can generally print normally, the reasonable emulsification value of ink, with water accounting for about 20-25%, is determined solely by the operator‘s skills and experience without instruments in China. This includes unstable factors and increases the possibility of malfunctions.
The water used in offset printing is not pure water. PVA plate water contains phosphorus and chromic acid, which corrode the plate greatly. It not only corrodes the sand mesh in the blank part of the plate, continuously increases the salt layer of the printing machine, but also corrodes the base paint of the graphic and textual parts, resulting in a decrease in the printing plate‘s durability. The wetting powder added to PS plate water contains more than ten chemical components and is a slightly acidic wetting agent with cleaning effect, which has extremely low corrosiveness to the printing plate.
Printing pressure
Printing pressure is also a major foundation of process technology. Offset printing is an indirect printing process where the image is transferred from the plate cylinder to the blanket for the first impression. After the blanket cylinder receives ink, the imprint is transferred to the substrate. This is the second impression, and the pressure required for the two impressions is different. To achieve the state of ‘ideal pressure‘, more effort is needed.
The pressure between the plate cylinder and the rubber cylinder in a general offset printing press is about 0.10mm; The pressure between the rubber cylinder and the impression cylinder is about 0.20-0.25mm. With the adoption of PS plates with good flatness and imported air cushion rubber blankets, the pressure between the plate cylinder and the rubber cylinder can be reduced. For example, the imported Heidelberg four-color machine can print at 0.05mm.
The pressure used in offset printing is achieved by calculating the drum radius, measuring the center distance, and adjusting the number of padding. The pressure of offset printing must be standardized and controlled with data. It is not allowed to arbitrarily increase the lining or blindly increase the pressure, resulting in sudden changes in pressure, uneven linear velocity on the roller surface, increased friction on the contact surface, and even other faults such as grease, ghosting, ink bars, etc.
Therefore, the correct use and adjustment of printing pressure is an important part of the process technology required for printing products.
Inaccurate overprinting
Overprinting inaccuracies can be divided into two categories: vertical overprinting inaccuracies and horizontal overprinting inaccuracies. There is a saying that says‘ if the paper is firmly controlled during transportation, it can ensure accurate printing. ‘However, this statement is not comprehensive.
For example, if the embossing grinding shaft or sleeve is worn, although it can be firmly controlled during paper transmission, it cannot achieve correct control. This is like a person holding a ball in both hands, with both arms straight and bent, but the distance and stability of the ball held in two different positions from the human body are different. So it should be said that ‘correct and firm control is necessary to ensure accurate overprinting‘.
There are many reasons for inaccurate overprinting, common ones include: paper stretching, paper feeding deviation, inaccurate positioning, insufficient biting force, worn biting shaft, non compliant handover, and worn transmission components of the paper feeding teeth.
In addition, some special factors can also cause inaccurate registration, such as large deformation of the rubber layout, which can also result in inaccurate local registration of the image; The axial movement of the paper transfer teeth shaft and the embossing cylinder shaft can cause inaccurate lateral overprinting.
Color sequence arrangement
In the past, the printing color sequence of monochrome machines was always in the order of yellow, red, blue, and ink. The biggest difficulty in this color sequence arrangement is to sign off on the printing samples of yellow and red plates, especially the first color yellow plate, which is related to the color reproduction and replication effect of the printed product.
If the yellow plate is printed too deeply, the skin color of the characters will lack vitality, and the houses will be as old as ancient temples, making it difficult for people to accept; If the yellow version is printed too lightly, the copied image will be dry and dull, with a color tone leaning towards blue and purple, which is also not aesthetically pleasing.
There are two main reasons for the color deviation of the yellow label sample: firstly, the retinal color recognition cells of the human eye have the lowest ability to distinguish yellow; The second issue is that people are not very familiar with the oil absorption of paper, and there is a lack of instruments to detect it. Controlling the same size often leads to the drawbacks of being too deep or too light.
The color sequence arrangement of the two-color machine can place the yellow and blue plates in the same printing process, with the blue plate serving as a filter for the blue glass, making it easier to identify whether the ink layer thickness of the yellow plate is appropriate. However, due to the wet stacking wet printing process, the dual color machine often produces irregular A and B double images at the two corners of the trailing edge, which requires appropriate changes in color sequence during process arrangement to solve the problem.
For multi-color offset printing machines with four or more colors, due to the wet stacking and printing of three colors, the color sequence is arranged from high to low based on the viscosity of each ink color. Otherwise, reverse printing failure may occur, resulting in the color mixing problem of dark ink color. Sometimes the first few colors may also produce A and B double images, and the color sequence needs to be adjusted as necessary.
Shenzhen Gold Sun Color Printing Factory is a China based book manufacturer, very good at printing hardcover book, photo book, story book, photo album, Printing paper, coloring book, packaging & printing services, Labels, printing stickers, anti-water labels, vinyl label, custom label book , softcover book, custom book printing hardcover, mini book, photobook printing, hardcover book, , board books, color sticker books, sticker books, packaging boxes for small business, custom book, children board books, kids book, journals, notebooks, Agenda, Customs Calendar, magazines, color books, cookbooks, etc. With ISO-2001 and CE certificate, Gold Sun offers very good price and outstanding service.
Welcome contact us through admin@goldsunprinting.com or add whatsapp +86 13802583954. Thank you.