Pre Printing Surface Treatment of Paper
Time:2025-04-10
Views:774
Firstly, from a business perspective, surface treatment is a method of providing added value to paper and cardboard products. Secondly, it can also be said to be a method of reducing the net cost of materials. In fact, from a material perspective, it is a method of modifying paper and cardboard by providing strength properties, such as;
Strength performance --- stiffness, tensile strength, and compressive strength
Optical performance --- whiteness, brightness, opacity
Absorption Performance --- Wettability and Absorption
Surface properties --- roughness, smoothness, and friction performance.
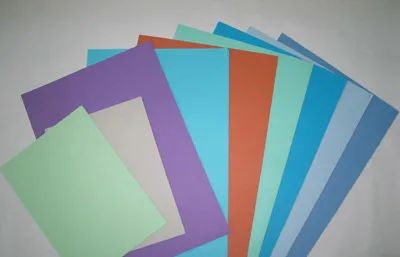
humidifying treatment
The deformation of paper includes force deformation and natural deformation. Natural deformation is mainly caused by moisture content. As the main component of paper is cellulose, which contains multiple hydroxyl groups in its structural formula, these hydroxyl groups determine its strong hydrophilicity; In addition, there are gaps between paper fibers and between fibers and fillers, and these pores have an adsorption effect on water. After absorbing moisture, the fibers of the paper will expand, causing the size of the paper to increase. After high-temperature dehydration, the size of the paper will decrease, which will affect overprinting.
If the moisture content of the paper is too high, it will reduce the surface strength of the paper. In light cases, there may be individual fibers being connected during printing, commonly known as pulling, while in heavy cases, there may be a peeling phenomenon of whole fibers being connected. Low moisture content makes the paper hard and brittle, reducing tear resistance, folding resistance, and bursting resistance, making it difficult to transport and receive paper, and difficult to accurately register. In order to make the moisture content of the paper uniform and suitable for the printing workshop, reduce the sensitivity of the paper to water, and improve the stability of the size, it is necessary to carry out moisture adjustment treatment before printing.
Humidity control treatment is the process of hanging and drying paper in a drying room at room temperature and pressure, with a certain relative humidity. After a period of time, the moisture content of the paper is balanced and adapted to the temperature and humidity of the printing workshop. The methods include: equal humidity adaptation method, moisture absorption method, moisture removal method, cold water reprinting method, etc.
Coating surface treatment
The application of most surface treatments is to lay the foundation for further coating outside the machine, especially to improve positioning control, that is, Z-direction coverage ability and surface performance, as well as X-Y direction variability. Raw paper is an important factor that affects the surface treatment effect.
The positioning "control" effect depends on the original paper itself. Proper control of the properties of the base paper remains a challenge in surface treatment. Although surface sizing can control wettability and absorbency, it does not significantly improve the unevenness during forming and the appearance of the paper. And these structural properties determine the uniformity of the paper: the surface structure deforms at the bottom of the forming process.
The importance of consistency in the base paper lies in the magnitude of the pressure applied during the final coating process. For sizing press, roller coating, and scraper or scraper metering coating, the pressure is relatively high. It determines whether changes in coating thickness and uniformity can produce qualified products. In the future, advanced real-time testing methods and data organization equipment will be used to record parameters such as surface distribution, uniformity, and permeability.
If the pre pressed light causes the surface to bend towards the direction of the floc structure, then the other advantages of pre pressed light are limited. Although roughness fluctuations may be reduced, calendering cannot change the variation of roughness in the X-Y direction, and the surface is still uneven. In addition, calendering may cause local changes in paper tightness, absorbency, and surface consistency, which can affect coating structure and uniformity.
Functional Coatings
Not all coatings require dyeing, and the development of adhesives, protectants, and peelable coatings typically begins with in machine application of surface sizing agents (etherified starch or esterified starch, alginate, and polyvinyl alcohol). Whether it is silicon peel coating, adhesive and protective coating, they all improve the coverage ability and economy of functional coating layers. The control of the coverage ability of any additional layer (whether it is silicon or printing ink) is a critical part of the coating function. Protective coated paper and cardboard have a wide range of applications, including food packaging paper, cardboard, labels, rolls, and packaging materials, as well as protective paper. Currently, most research is developing in this area.
Shenzhen Gold Sun Color Printing Factory is a China based book manufacturer, very good at printing hardcover book, photo book, story book, photo album, Printing paper, coloring book, packaging & printing services, Labels, printing stickers, anti-water labels, vinyl label, custom label book , softcover book, custom book printing hardcover, mini book, photobook printing, hardcover book, , board books, color sticker books, sticker books, packaging boxes for small business, custom book, children board books, kids book, journals, notebooks, Agenda, Customs Calendar, magazines, color books, cookbooks, etc. With ISO-2001 and CE certificate, Gold Sun offers very good price and outstanding service.
Welcome contact us through admin@goldsunprinting.com or add whatsapp +86 13802583954. Thank you.