Common measures for controlling imprint deformation in offset printing
Time:2024-10-29
Views:776
Preventive measure
To avoid imprint deformation during the printing process, prevention is the first step. Preparation should be made before printing to prevent imprint deformation.
(1) For paper with poor quality and easy to stretch and deform, it is best to wet it before printing. The most effective method is to first coat the problematic paper with clean water, then roll it with a roller and coat it with clean water. After that, the moisture content of the paper will be more uniform and stable. When printing on the machine, the problems of stretch and fan-shaped expansion of the imprint will be greatly improved. If possible, it is recommended to use this method to solve the problem of stretch deformation caused by paper quality.
(2) When printing on the machine, try to arrange the direction of the paper fibers parallel to the axis of the drum as much as possible, so that the direction of the coming and going imprints is not easily changed, and the fan-shaped phenomenon of the imprints is not easy to occur. Even if the size direction of the imprints (the direction of drum operation) is elongated, it can be remedied by changing the drum lining and pulling plate. In addition, during the first color printing, an additional 0.05mm lining can be placed under the printing plate in advance to reduce the size of the text and images.
(3) When making a plate, arrange the theme part of the image at the mouth or near the side gauge; When printing, place colors with high registration requirements in adjacent color groups, which is beneficial for the registration of the main graphics and text.
(4) Regularly check the paper holding condition of each tooth row‘s paper holding teeth. If it is found that the paper holding teeth are worn or damaged and cannot be opened or closed properly, adjustments should be made before printing. When printing paper of different thicknesses, the gap between the front gauge and the paper feeding table, the gap between the paper feeding pad and the paper feeding table, the gap between the paper feeding pad and the embossing cylinder, the cylinder lining, and the printing pressure should all be adjusted accordingly. If you want to use a single or dual color machine to print colored parts, generally do not adjust these parts randomly during the printing process. If there are special problems that must be adjusted, the semi-finished products should be marked separately, and attention should be paid to observing whether there is any change in the imprint after adjustment.
(5) When selecting a rubber blanket with good printing adaptability, the radial direction with low elongation should be chosen as the tightening direction (the direction of the rubber blanket is usually marked on its back), and it should be cut into a square rectangle without any skew. When installing the rubber blanket, it is necessary to gradually and evenly tighten it back and forth. You can use your fingers to tap the edge of the rubber blanket to check if the tightness is appropriate and even, and it is advisable to hear a crisp sound.
(6) During the printing process, it is necessary to properly prepare the dampening solution and control the moisture content of the plate. The minimum amount of water should be used while ensuring the cleanliness of the plate to prevent excessive water absorption and deformation of the paper.
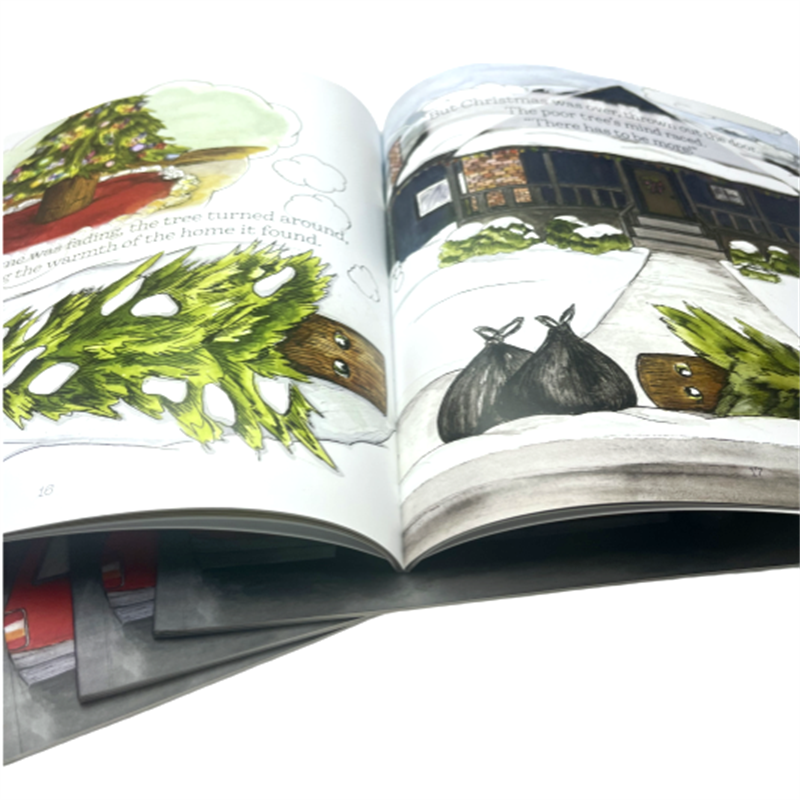
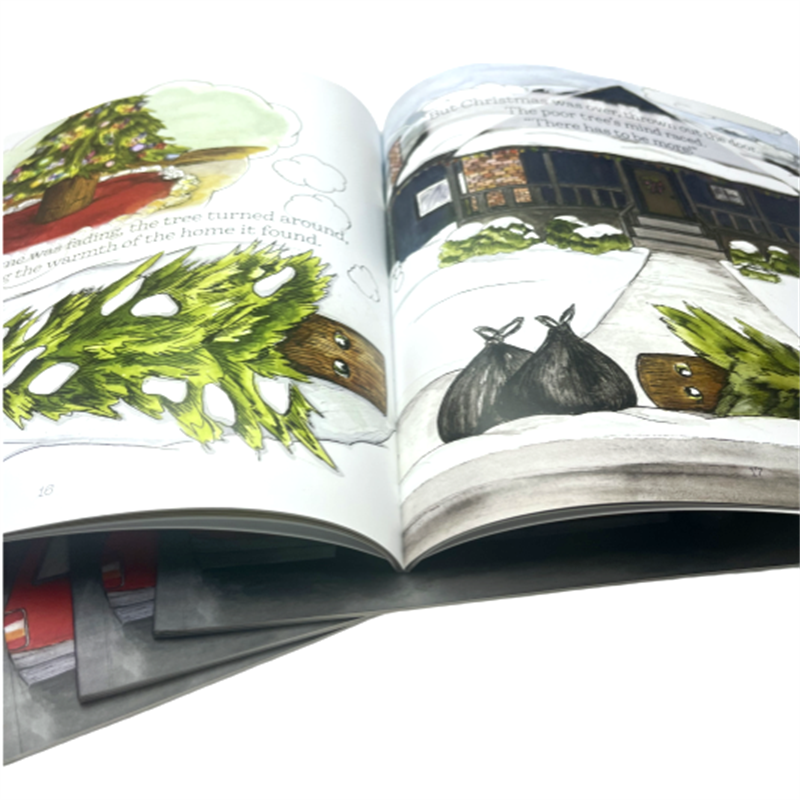
Improvement measure
If the imprint is found to be fan-shaped during the printing process, the following measures can be taken.
(1) The gripper teeth of the first color embossing cylinder bite the paper normally, while the gripper teeth at both ends of the second to fourth color embossing cylinders gradually reduce their biting force, with the aim of compensating for the fan-shaped expansion of the imprint after the previous color group embossing.
(2) Most offset printing machines have a plate clamp at the trailing end that is divided into two sections, with an adjusting screw in the middle and top screws at both ends. If the first color is tilted, the printing plate can be tightened inward by using the screws on the support heads at both ends of the plate clamp. The second to fourth colors can be expanded by adjusting the screw in the middle of the plate clamp according to the printing situation. This expansion and tightening of the plate can be operated within 0.30mm, and excessive expansion can cause the plate to crack.
In short, when there is a problem of imprint expansion and contraction, it is necessary to carefully observe and distinguish what factors are causing it, and take corresponding measures to deal with it. Generally, imprint expansion and deformation faults can be effectively solved. As for the compensation methods such as expanding or tightening the printing plate, adjusting the degree of tooth biting force, etc., there is a certain limit to the adjustment amount, and excessive adjustment can cause other problems. For paper with poor quality, severe stretching and deformation, and inability to meet printing quality requirements, it is recommended to switch to paper with good printing adaptability for machine printing.
Shenzhen Gold Sun Color Printing Factory is a China based book manufacturer, very good at printing hardcover book, photo book, story book, photo album, Printing paper, coloring book, packaging & printing services, Labels, printing stickers, anti-water labels, vinyl label, custom label book , softcover book, custom book printing hardcover, mini book, photobook printing, hardcover book, , board books, color sticker books, sticker books, packaging boxes for small business, custom book, children board books, kids book, journals, notebooks, Agenda, Customs Calendar, magazines, color books, cookbooks, etc. With ISO-2001 and CE certificate, Gold Sun offers very good price and outstanding service.
Welcome contact us through admin@goldsunprinting.com or add whatsapp +86 13802583954. Thank you.